The power plant’s down, but the lights are on
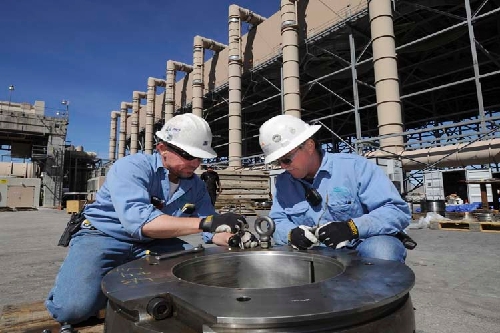
Nevada’s biggest power plant is offline, and you haven’t even noticed.
Credit 18 months of planning and a logistics operation to rival the staging of a small convention.
For the first time ever, NV Energy’s Chuck Lenzie Generating Station 20 miles north of Las Vegas is completely closed, as the 6-year-old plant undergoes an overhaul. To carry out the rehab, NV Energy laid asphalt staging zones, brought in 350-ton and 60-ton cranes and boosted the plant’s workforce from its usual 30 to 200. The plant’s 40 days off line between March 9 and April 20 are “an eternity” in an industry where most maintenance outages last five to 10 days, said Kevin Geraghty, NV Energy’s vice president of power generation.
Lenzie’s load of 1,102 megawatts — about what it takes to power the Strip — has shifted to other generating stations, which can handle the capacity when there’s low seasonal demand for cooling power.
To understand the significance of Lenzie’s makeover, start with how the natural gas-fueled plant works.
The plant adds natural gas to compressed air and sparks the mixture to create fire. Pressure from the fire turns a turbine connected to a generator, which produces electricity. At Lenzie, a second stage captures waste heat from the first phase and turns water into steam to spin another turbine linked to a generator.
The process puts intense pressures on Lenzie’s mechanical systems.
The plant’s four natural-gas turbines and two steam turbines operate on jet engines that run at 250,000 horsepower. In comparison, an engine on a Boeing 767 generates 90,000 horsepower on takeoff and 43,000 horsepower in flight, Geraghty said.
The turbines spin at 3,600 revolutions per minute, and the blades’ outer edges reach the speed of sound at full-tilt. Throw in blasts of air at temperatures of 1,100 F, plus steam that reaches 3,000 F, and the sheer physical forces constantly pulling and pushing at Lenzie’s components can over time wreak havoc on the plant’s efficiency.
So after every 48,000 hours of operation, the plant needs a total makeover costing $10 million to $20 million.
What’s happening through late April is essentially a frame-up restoration led by General Electric, which made the plant’s turbines. Every valve, pipe, generator and water drum at Lenzie is getting the once-over. Each turbine is being dismantled blade by blade and bearing by bearing to look for pits, cracks, warping and mineral build-up.
Potential flaws can be so small that they’re visible only via X-ray or the kind of ultrasound machine that detects plaque buildup in your arteries. Miss a tiny but fatal flaw in a blade that then gives out while a turbine is running, and the resulting damage could knock the machine out of commission for repairs for months, said Forrest Hawman, Lenzie’s operations and maintenance manager.
Some fixes are simple. Sandblasters can peel off mineral buildup, for example. But other components need more intensive retooling, and will be sent to a GE factory in Salt Lake City for repair. Some parts are replaced altogether.
Once Lenzie is put back together, Hawman said, its efficiency levels will be virtually indistinguishable from efficiencies the plant enjoyed when it was new — just in time for summer.
Contact reporter Jennifer Robison at jrobison@review
journal.com or 702-380-4512.