Lithium ion batteries boost Nevada education and related industries
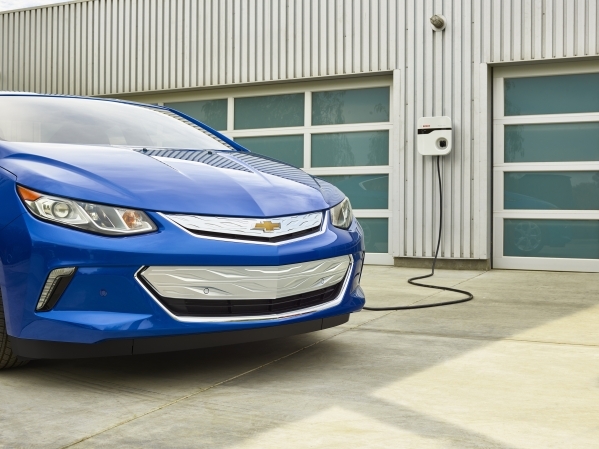
The University of Nevada, Las Vegas received a million dollar grant from Tesla Motors this month that will endow the university to ramp up research efforts over the next five years. Faculty and graduate students will study innovative ways to enhance the production of lithium-ion battery cells and integrated battery storage packs, in partnership with the Tesla Motors gigafactory at the Tahoe Reno Industrial Center in Storey County.
“Our faculty are performing high-caliber research and are enthusiastic about collaborating with a leader in the electric vehicle manufacturing industry,” said UNLV President Len Jessup.
One research team will focus on water recycling and treatment at the gigafactory, while a second team will focus on salvaging and recycling metals from within the lithium-ion battery cells once they have reached end-of-life.
Just 18 months ago, Tesla Motors CEO Elon Musk outlined an ambitious and radical concept for a gigafactory that would produce billions of lithium ion battery cells and integrate them into battery packs under one very large factory roof. Large economies of scale, coupled with streamlined automation, were projected to drive down multiple process costs for lithium-ion electric car batteries by over 30 percent.
Musk envisioned a production goal of 500,000 finished battery packs per year, in order to ramp up battery pack production for the company’s Model 3 mass market automobile. During 2014, these projections of the scale of battery cell and pack production at the gigafactory would have effectively doubled the production of the entire existing lithium-ion battery industry at that time.
Nevada, Arizona, New Mexico, Texas and California were considered as competing host states for the gigafactory, but Nevada had a few aces to show when the states’ negotiating teams put their cards on the table.
Other than California, Nevada was the closest state to Tesla’s electric car production factory in Fremont, Calif., with highway and rail transportation already in place and more infrastructure development by the Nevada Department of Transportation underway.
The Tahoe Reno Industrial Center in Storey County could already provide a huge real estate parcel that had been developed specifically for warehouses and manufacturing. The Storey County government also offered a minimal permitting process that allowed Tesla Motors the opportunity to begin scaling its gigafactory without delay.
Nevada is home to the largest lithium mine in the U.S., 225 miles southwest of Storey County in Silver Peak. The Albemarle/Rockwood Lithium mine sits atop an extinct volcano in Esmeralda County.
Bubbling hot springs have pushed up briny water into aquifers near the earth’s surface that are relatively rich in concentration of lithium minerals. Compared to hard rock mining, the Silver Peak mine uses a more low-tech and cost-effective extraction process, by pumping up the brine from the aquifers into into surface evaporation ponds. The hot desert sun evaporates the liquid away and the mineral concentration can be increased by combining the contents of several ponds.
Mix in soda ash to create lithium carbonate or add limestone to make lithium hydroxide. Both resulting powder compounds can be used to manufacture the cathode of a lithium-ion battery cell.
The Silver Peak mine has been operating for more than 50 years, since it was first established by the Foote Mineral Company in the 1960s. Unlike gold or silver mines, lithium mines can continue to harvest brine resources over a sustainable period of time, as long as volcanic hot springs continue bubbling up from the earth’s core to replenish the underlying aquifer from below. Geothermal hot springs also provide an ongoing source of power that can be tapped to provide steam and electricity generation for the pumping system.
Albemarle, a chemical engineering company based in Louisiana, recently purchased the Rockwood Lithium facilities in Silver Peak and its even larger sister mine on the Salar de Atacama in Chile. The company is betting on the growth of the lithium battery industry and is now vertically integrated to provide battery-grade lithium carbonate or lithium hydroxide from its mining operations, as well as the essential cathode component and other chemical ingredients for lithium-ion battery cells.
Tesla Motors has also been signing development contracts with other lithium mining operations, both in Nevada as well as outside the state.
Pure Energy Minerals from Canada recently inked a development agreement with Tesla Motors and has staked out a claim adjacent to the Albemarle/Rockwood Lithium mine. The company has some innovative ideas of its own to speed up the brine harvesting process and increase the rate of battery-grade lithium production, while maintaining a cost-effective mining operation.
Other worldwide battery manufacturers have not been standing still since the announcement of the Tesla Motors gigafactory.
This month, General Motors and LG Chem in South Korea projected that they could provide lithium-ion battery packs for the Chevrolet Bolt electric car at $145 per kilowatt-hour to manufacture. The anticipated release date for the Chevrolet Bolt has still not been announced, but automotive industry analysts predict that the all-electric car could be available to consumers sometime in 2017.
The electric Bolt will be able to travel more than 200 miles on stored energy from its lithium-ion battery pack at a price tag of about $30,000. LG Chem also projected that its company could drive down battery storage costs even further to $100 per kilowatt-hour by 2021.
Just three years ago during July 2012, the cost of manufacturing a lithium-ion battery pack was about $600 to $700 for every kilowatt-hour of electric energy storage capacity produced. McKinsey & Company at that time forecast that improvements in lithium-ion battery technologies might drive the cost down to $200 per kilowatt-hour by 2020, maybe even to $160 per kilowatt-hour by 2025. The lithium-ion battery manufacturing industry has already exceeded that benchmark.
Gigafactory construction plans have also been announced this year in China and Japan, to produce billions of lithium-ion cells at each location.
The good news for Nevada is that as long as the demand for lithium-ion battery cells continues to grow within the automotive, renewable energy, building construction, and utility grid markets, multiple industries and institutions within the state will benefit.